Corumat’s Food Waste-Derived Packaging Challenges Traditional Plastics
West Coast-based tech startup Corumat is making packaging from postconsumer food waste. The products use about one-third the material typically incorporated in conventional plastics. They are heat stable; break down faster; and are cost-competitive with molded fiber and solid plastic takeout containers.
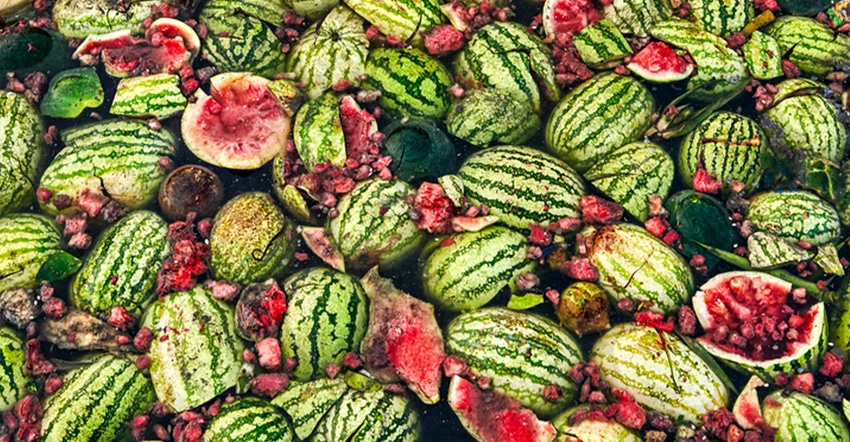
West Coast-based tech startup Corumat is making packaging from postconsumer food waste. The products use about one-third the material typically incorporated in conventional plastics. They are heat stable; break down faster; and are cost competitive with molded fiber and solid plastic takeout containers.
Corumat has proven its technology at pilot scale working with research institutions and industry players in the commercial composting and fast-food sectors. The young company continues to take meaningful steps forward. Among its latest plans are to launch a 30,000-square-foot manufacturing facility in Yakima, Washington, as well as to begin work with petroleum giant Shell.
Mike Waggoner, founder of Corumat, shares some of the company’s story, pausing on his first big break. It came when the U.S. Department of Agriculture (USDA) offered him a pilot manufacturing facility and $700,000 to develop the packaging and to show it could be made from food waste, specifically that the organics would produce lactic acid, a carbon-negative organic chemical which is the main building block in Corumat’s products.
For now, the market forerunner in biobased plastics is polylactic acid (PLA), but this monomer has limitations. It’s slightly more expensive than conventional plastics and does not stand up to heat well. PLA can warp in high temperatures during transport.
Waggoner explains two primary differences in his products and how the technology works:
“Think of plastic like a pile of ropes. It acts like it does because of how well tangled together those ropes are. We are making crystals that are like organized piles of rope. Crystallization makes the material more heat stable.”
He also calls out the cellular structure, which helps to break down the packaging in less time than solid plastics. The makeup is similar to that of a sponge, which enables material-eating microbes to penetrate more areas and work faster.
“So, you have a triple positive effect where you use less material; it breaks down faster; and it’s better performing,” Waggoner says.
The process is unique in that it creates a material with a tough outer ‘skin’ that entraps an airy, foam-like inner layer, says William J. Orts, who leads bioproducts research at the USDA.
“When the biomaterial is discarded, the outer layer, once penetrated with even a pinhole, allows water, enzymes, and microbes into the accessible inner layer, which readily degrades the material from the inside, outward to meet compostability standards,” Orts explains.
Corumat’s material is certified by the Biodegradable Products Institute (BPI) and has also been tested in the field. At Cedar Grove, a large Seattle, Washington compost facility, it broke down in the operator’s required timeframe to make product.
The new Washington State processing facility will have the capacity to produce hundreds of millions of containers a year. Waggoner is in search of launch customers to run at that scale.
“So far, we’ve secured $5 million in grants to develop our products and perform pilots. But to enter large-scale production we will have to raise more private capital. You have to show investors you have interested customers,” he says.
The startup’s earliest lifts have come from its home state, the federal government, and even beyond U.S. boundaries. Major funders are the Environmental Protection Agency, the USDA, and the National Science Foundation. The Washington State Department of Commerce provided a state grant and Israel-United States Binational Industrial Research and Development (BIRD) Foundation has also backed Corumat.
On the research front pilot partners include what Waggoner describes as one of the top 10 fast food chains and one of the largest packaging companies. Neither could be named due to nondisclosure agreements.
A collaboration with California State University (CSU) Chico produced lightweight cutlery prototypes with as little as half the material of conventional compostable cutlery but was strong enough to cut through a cardboard box.
Takeout containers tested at a fast-food chain showed their insulation capabilities. Food stayed hot for up to four times longer than in paper.
The near future is looking bright as the tech company works to gain more visibility. It has been accepted into an incubator program funded by Shell in the petroleum giant’s pursuit of partners to help advance clean technologies and for help reaching its net-zero goals.
“We are especially excited to be working with Shell to scale our vision to divert food packaging and food waste from landfills and convert them both into more packaging,” Waggoner says.
A mechanical engineer by trade, what has become his niche seemed an unlikely path years ago. His thoughts turned to sustainable packaging when he was exploring ways to build machines to produce lightweight plastics that leverage high-pressure CO2.
His project was funded by a company that was trying to make plastic foams from recycled materials.
“They are very hard to recycle, and I realized it was never going to work, but some of their customers were asking if a product could be made using PLA,” Waggoner recalls.
His thoughts increasingly turned to the products themselves, not just the machines to make them. From there came the idea for his early prototype, and that’s when the ball started rolling.
Transitioning away from fossil-derived packaging will take plenty more work. Waggoner and other entrepreneurs trying to crack bioplastics see a potential policy break around the bend. The Biden Administration announced an executive order calling for 90 percent of petroleum-based plastics to be replaced with biobased polymers over the next 20 years.
“That’s an ambitious goal—a goal that could open up promising funding opportunities. This is an exciting time to be working to advance biobased plastics,” he says.
About the Author(s)
You May Also Like